packing
Packing
When looking for a packaging solution, you must first define the parameters of your production. From the nature of your product to the type of primary and secondary packaging, and the speeds of your production, all these factors will influence the final solution.
Packing machines use different approaches and technologies based on the true needs of each customer.
Nature Of Your Product
Different products require different approaches. While some products are robust and can withstand drops, others need finesse and care.
Bags of powder or frozen vegetables can withstand a drop with relative safety. These are the simplest to pack by opening a hatch and dropping them into their containers.
Glass and PET products, however, require more care and accuracy, which is why Pick & Place Packers are the right answer.
But not all pick & Place packers are created equal, and some machines are too aggressive for dairy products like yogurt (Zabadi). In such cases, Robotic packers offer smooth and fast motion, away from any jerkiness.
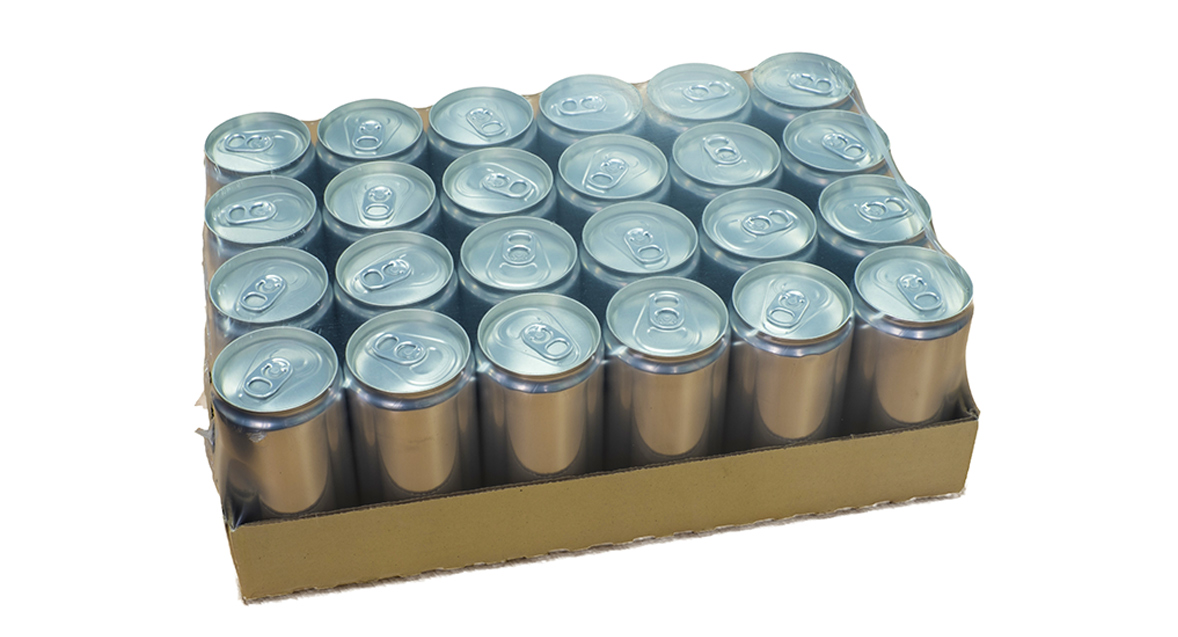
Secondary And Tertiary Packaging
Some exceptions exist (PET water bottles in RSC cartons), but the industry has established practices. These practices take into account the entire logistics chain from production to retail.
Technica follows these practices to guide you to the correct machine for your product:
PET round bottles tend to be shrink-wrapped, with carton trays or pads for support or without. And in the case of dairy, the packs are placed in stackable plastic crates.
Plastic Cups have varying dimensions across their height. As a result, they must be placed in a tray to preserve their spacing.
PET oval or square bottles, especially larger SKUs, are placed directly in crates. The same goes for large tubs.
Carton boxes and small bags are often placed in RSC carton boxes. This application will need cartons erectors and sealers.
Production Speeds
In this consumer age, production speeds are ramping up to follow consumer demand. In the same vein, Technica ramped up its technologies to follow your demands for high-speed packing.
Increasing the speed settings on a machine can sometimes work. But structural and inertial limitations force us to find alternatives:
Increasing the number of picking heads: This allows us a near proportional increase between machine throughput and the number of picking heads. But as the number of heads increases, payloads have to decrease.
Upgrading the technology used: Gantry packers are simple and robust, but the high inertia stops it from unlocking its full potential. 2-axis delta robots are agile and light, allowing higher cycle times. If you still need higher throughput, adding an extra axis to the delta robot is the answer. 3-axis delta robots allow picking on the fly without any stoppage.
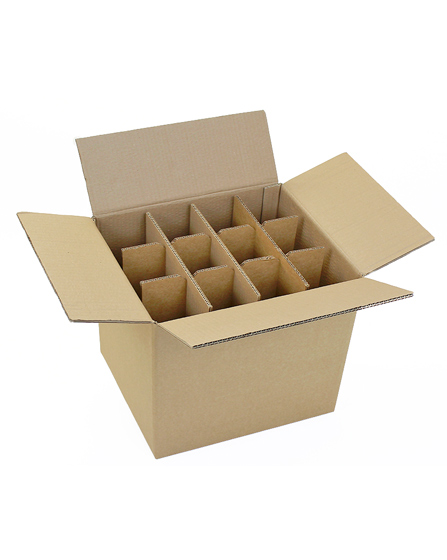
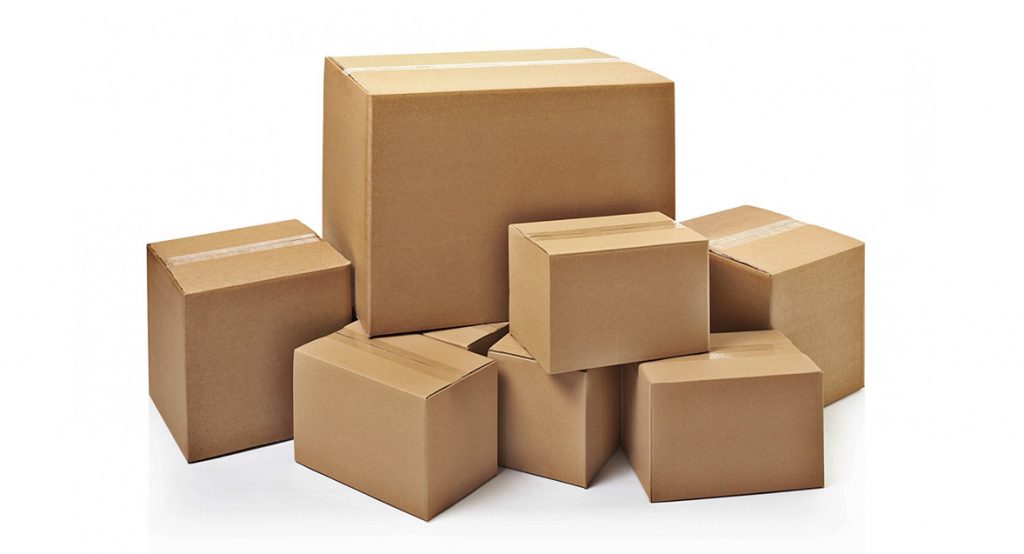
Footprint And Investment Cost
If your production does not require extreme speeds, you have an opportunity to achieve some savings. By combining machine functions into one block, you can save valuable footprint and initial investment.
Technica’s tray packer and crate packer can be merged into a single machine that can offer all functionalities (Tray packing, Crate Packing, combined packing) for maximum flexibility in half the factory space.
No need for independent carton erectors and sealers, Technica combines them in the same bloc as the Packer for optimized footprints.
Make sure to visit our packers portfolio (Link to the packers section)